100個の部品製作
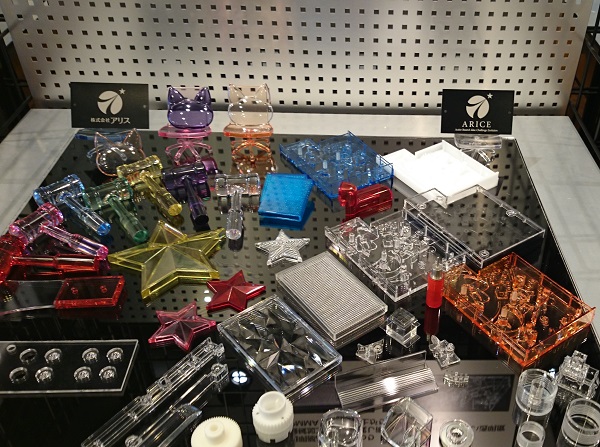
よくある100個ぐらいで部品を製作したいというご要望が、いつも
悩ましいです。
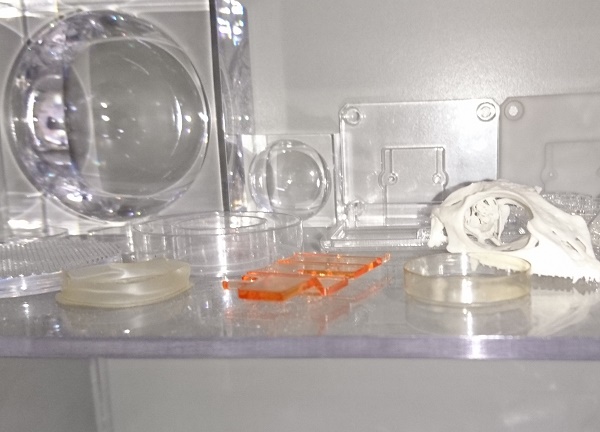
外径カットや穴加工、ザグリなどがあるFAライン用治具やワッシャー、
スペーサーや単純形状部品は切削加工でも時間が掛からず、数百円や
数千円などの低価格で部品を切削加工で製作できます。
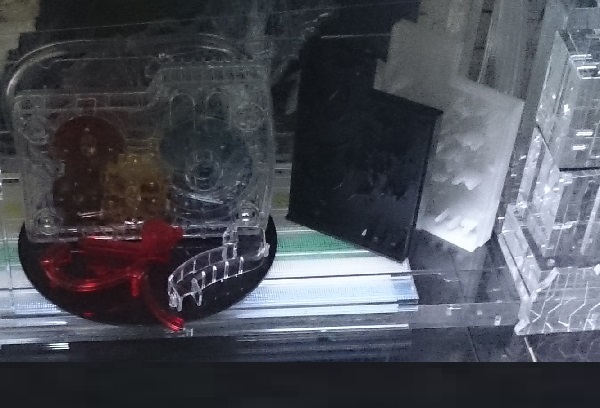
壁が高いとか多面加工が必要であったり、加工時間や手間が掛かる
部品形状を機械加工で製作すると、コストが合いません。
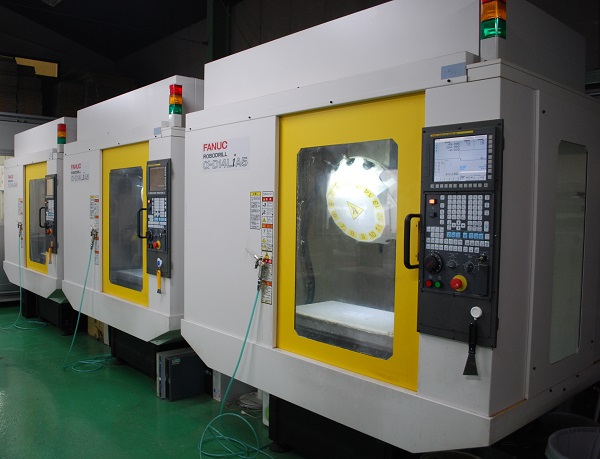
そこでプラスチック樹脂ならば射出成形や圧縮成形、アルミや亜鉛ならば
ダイカスト、銅や鉄、ステンレスならば押出成形や板金プレスなど
金型を製作して量産する方法を選びます。
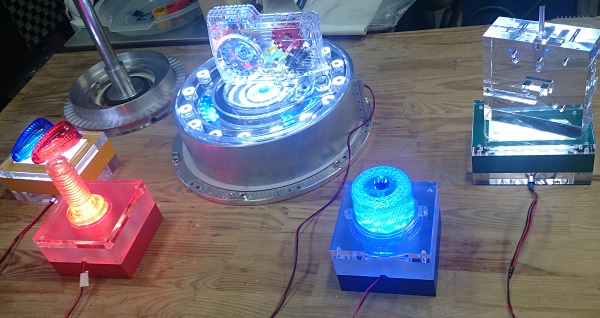
発注ロッドが1,000個以上であれば、数回の発注でコストは下がり、
金型費を償却できるのですが、100個の発注ロッドではなかなか部品の
製作コストが下がりません。
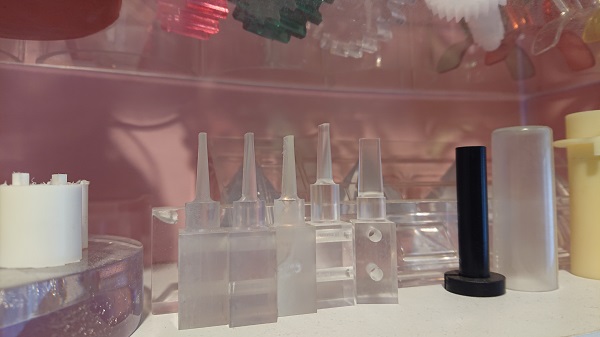
100個の発注ロッドでは、ほとんどの場合が最初がマイナスで、ある数量を
販売してからグッと利益が出てくるようになります。
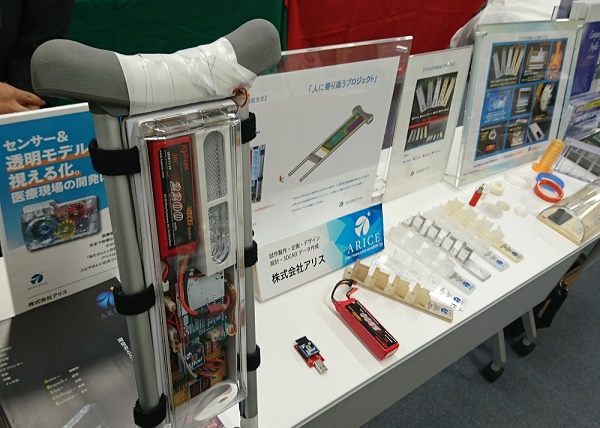
コストを抑えるために最初は少なく、売れてからたくさん製作する。
誰しもがそう思いますが、実際は儲かるところまで売るぞと覚悟して
開発商品などを製作する事になります。
自分が開発に投資するつもりで対応しています。
お気軽にお声かけ下さい。
開発ものづくりのプロフェッショナルとして
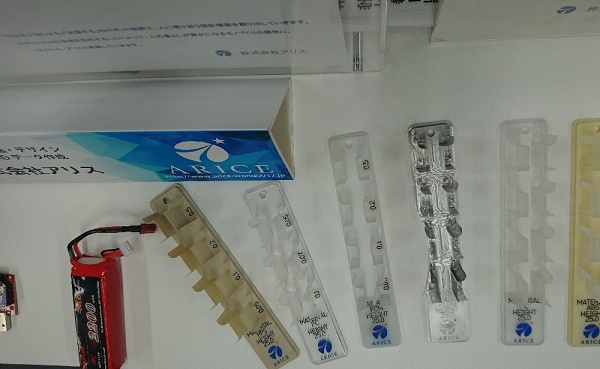
研究開発では、様々な素材やデザイン、機構や機能などが模索されています。
量産性も含めた最適を選択していくプロセスが新製品の開発です。
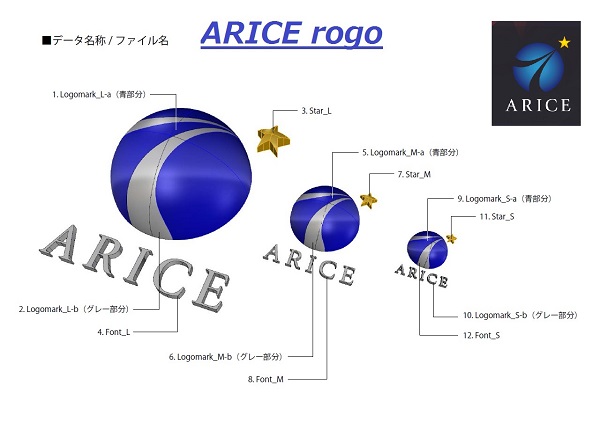
売れる付加価値の高い商品ほど、開発プロセスで解決すべき課題が多く、
設計を検証するための試作品が製作されています。
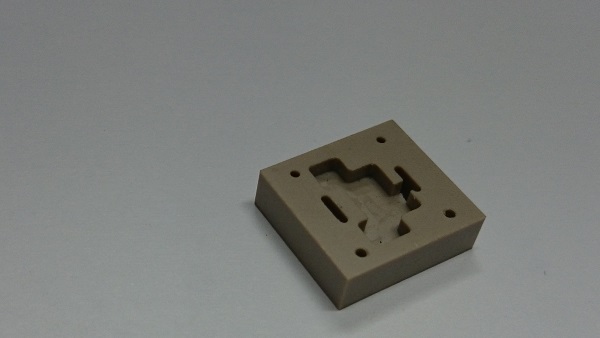
そういった先行開発や原理試作段階からの対応をしています。
最初から対応しているので、試作や量産試作、量産なども考えた
開発ものづくりをスムーズに進めていけます。
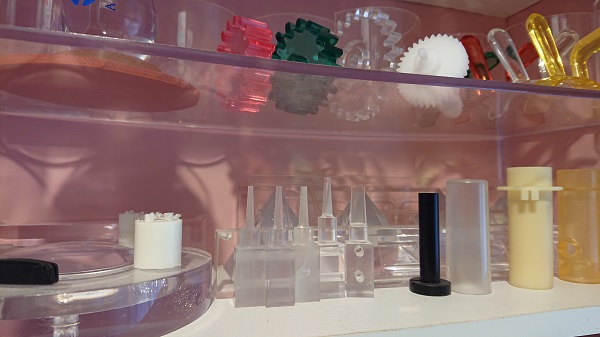
新素材の情報も豊富にあるので、その環境に適して材料のご提案も
できます。
開発段階からの開発ものづくりはぜひお任せ下さい。
プラスチック樹脂のオーダーメイド加工に対応
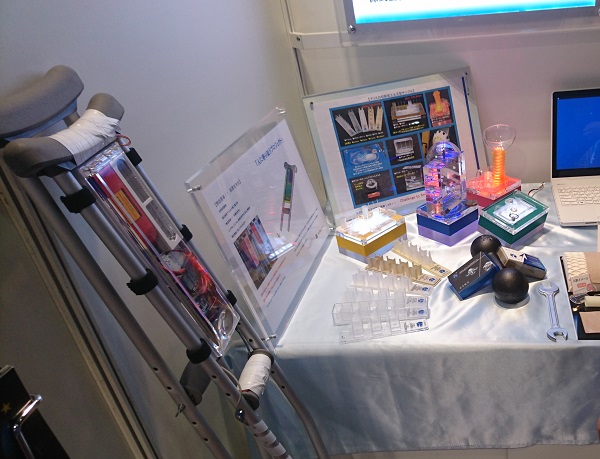
アイデアの段階から量産まで開発ものづくりに対応しています。
オーダーメイドの部品加工も得意です。
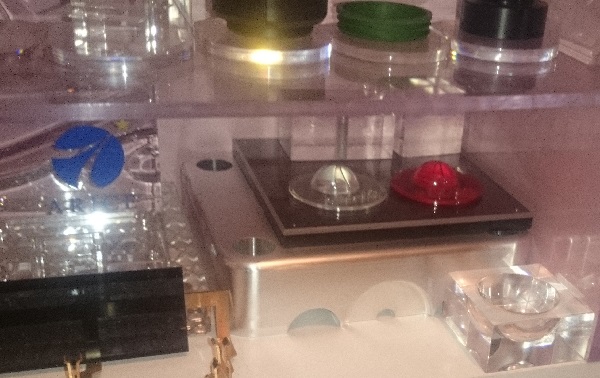
現物を持ち込まれたり、スケッチやご自分で製作された試作品など
から本格的な3Dデータを作成して試作から量産まで対応しています。
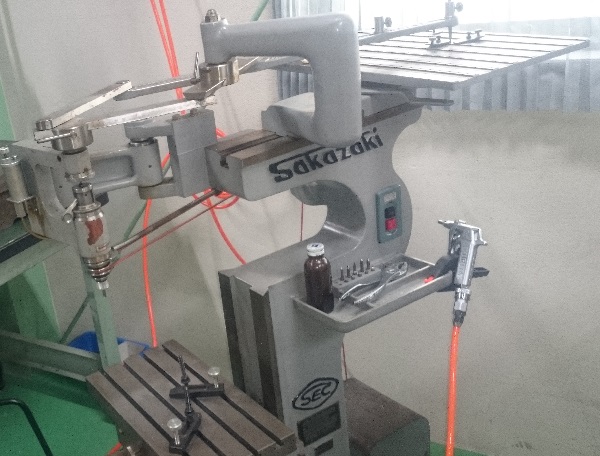
数が少ないと割高にはなります。
個人さんで試作を数百円や数千円でできると考えられている場合が
ございますが、ほとんどは数万円以上掛かります。
場合によっては数十万、金型を製作すると数百万なんてざらに掛かります。
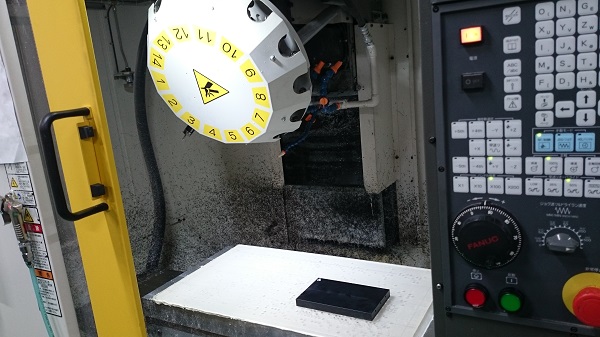
それなりの品質で開発するのであれば、高額なCAD/CAMや工作機械
を使って製作する事になります。
数百個や数千個を製作する場合は金型を製作することになりますが、
数十万ではなかなかできず、数百万にはなってしまいます。
よくある100円均一などは数十万個や数百万個を製作しているから
1個当たりの価格が安くなります。
数万個でも数量は多くはありません。
開発では、どれぐらいの数をミニマムロットとして発注するのか
が単価を決める事になります。
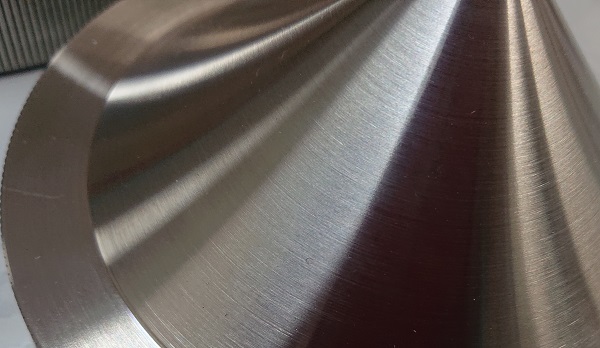
特に開発段階での試作などは量産のように自動的に製造ができません。
エンジニアや職人が手間暇をかけて製作する事になります。
材料も量産で使用する材料のように安価ではなく、高額です。
たくさん購入すれば材料は安価になりますが、試作で板を1枚とか購入
すると、驚く価格となります。
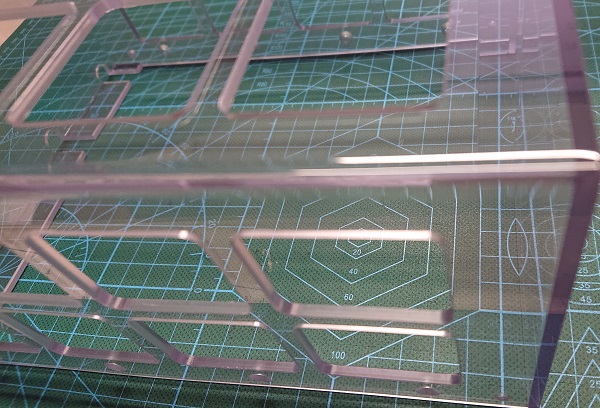
できる限りコストを抑えても、ある程度の開発費用は掛かります。
それが商品開発での大きなリスクであり、開発のプロフェッショナルである
メーカー様や商社様でないと簡単にアイデア商品を製作できません。
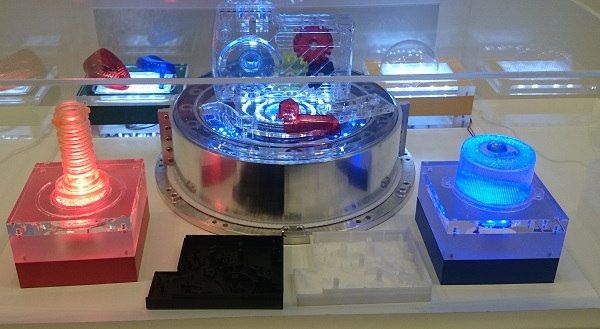
私たち(株)アリスは、最初に費用感をお伝えしています。
本当に簡単な形状やあり物の素材でしたら安価にできる場合もありますが、
プロフェッショナル向けとしているのは、開発費用の問題があるからです。
プロフェッショナルとして開発ものづくりに対応します。
お気軽にお声かけ下さい。
設計→試作サンプル製作→部品製作まで
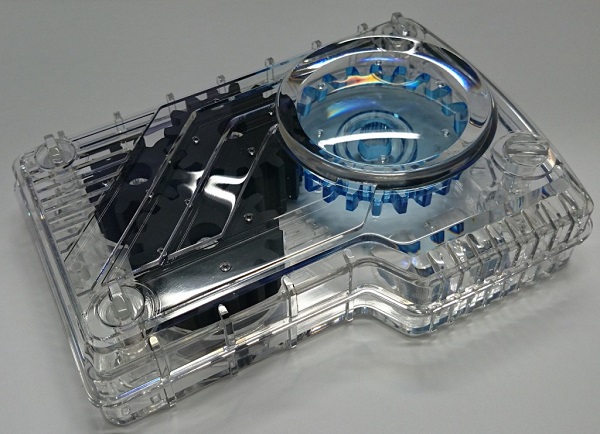
(株)アリスは、開発ものづくりのエンジニアリング会社です。
イメージだけのスケッチからでもご要望の部品を製作できます。
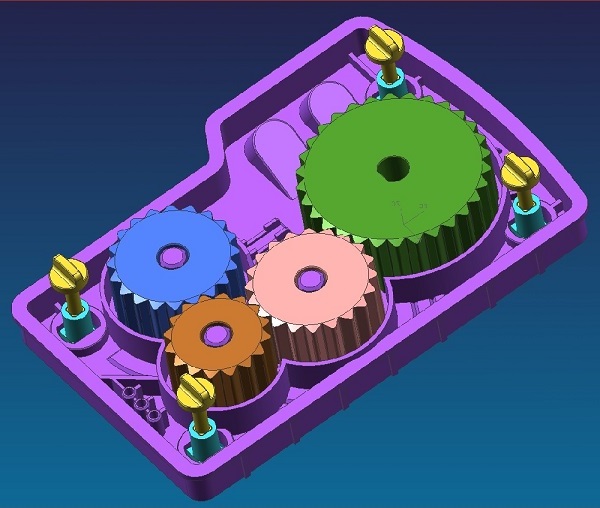
丁寧にヒアリングしながら、設計要素も含めて3Dデータを
作成していきます。
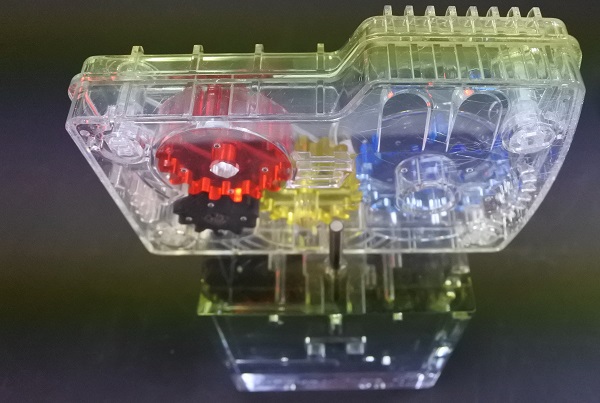
モデリング/プログラム/3D/2D/図面データの作成など、
それぞれの要素を得意とするCAD/CAMを使って開発ものづくり
を進めていきます。
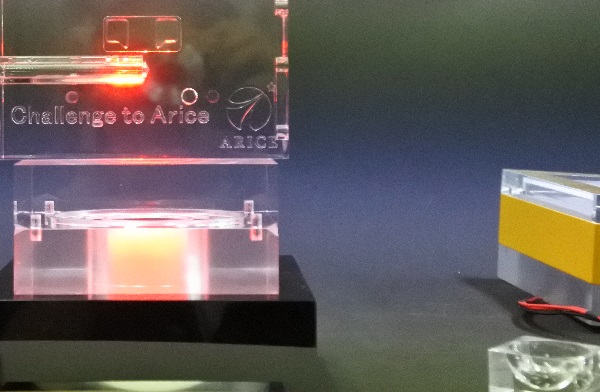
現物から、デジタルデータを作成して部品を製作するリバース
エンジニアも行っています。
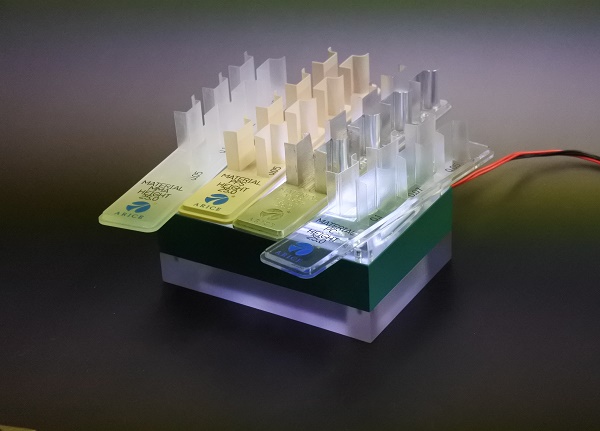
筐体設計や機構部品設計などを3Dデータで作成します。
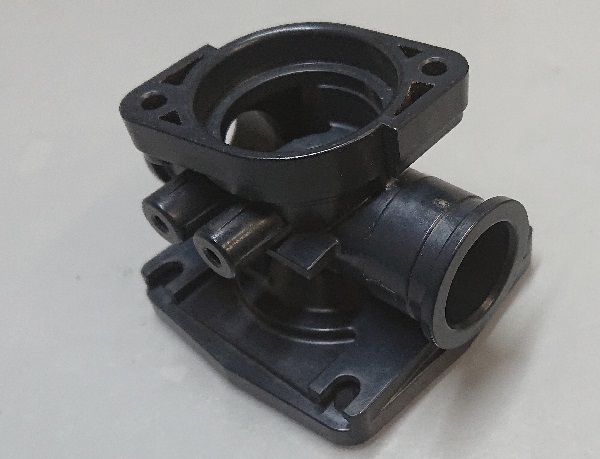
機構設計も対応しています。

それらを試作品で検証して、変更点を3dデータに盛り込み、
データを完成させます。
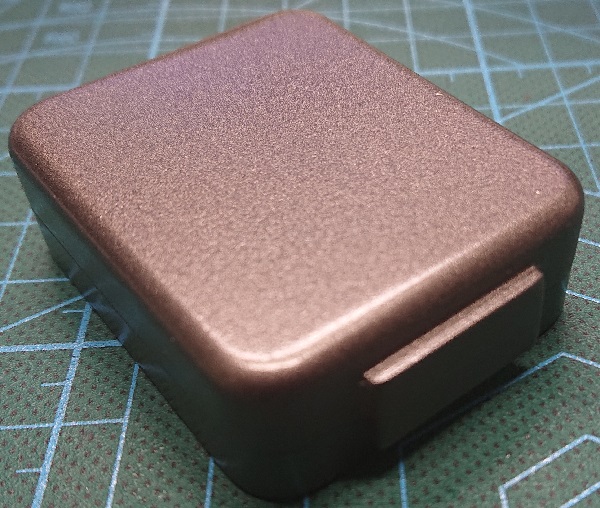
完成した部品データを量産部品の製造に向けたの作り込みを行います。
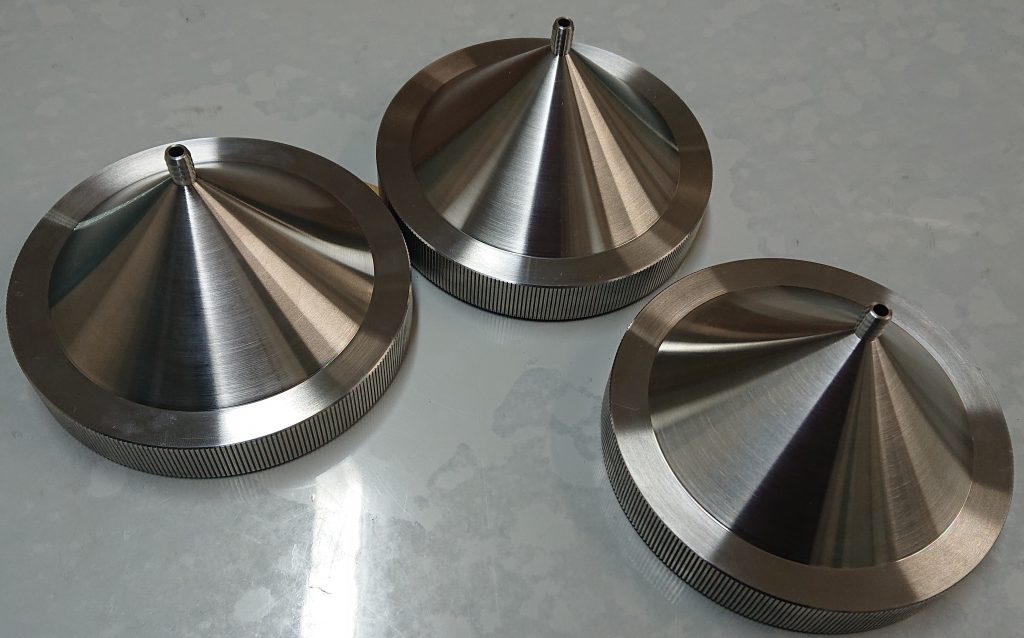
必要となる重要管理寸法図、組図なども作ります。
海外やお取引先で量産化するときに必要となります。
開発でのものづくりは、お気軽にお声かけ下さい。
コントロールとマネジメントのどちらを選ぶ?
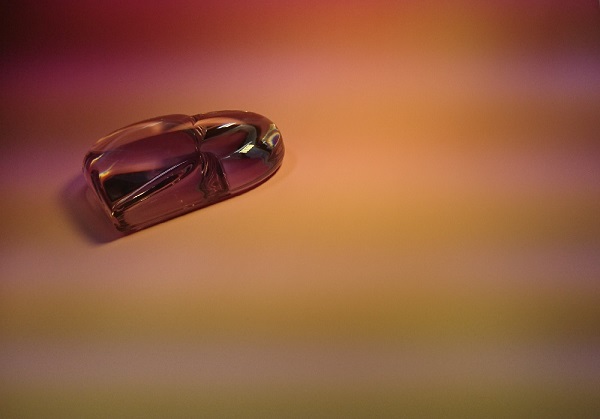
管理には、コントロールとマネジメントがあります。
コントロールは、コンサルタントのように、ゴールに到達
できる方法論を教えて実行させること。
マネジメントは、カウンセラーのように、自分で考えさせて
ゴールに導くこと。
ティーチングとコーチングとも言えるように思います。
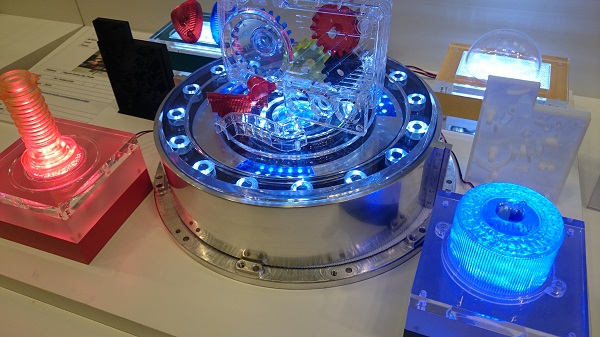
コントロールとマネージメントのどちらが良いのか?
ティーチングとコーチング のどちらがいいのか?
なんて議論や本をよく見かけます。
答えは、相手の状況によるという事だと思います。
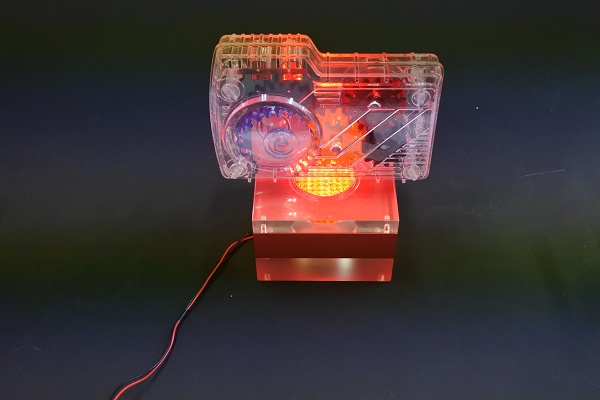
初めはコントロールが基本で、仕事を理解して、能力がある程度ついて
きたらマネージメントに切り替えて育てていく。
丁稚みたいな下積み時代も必要だと思います。
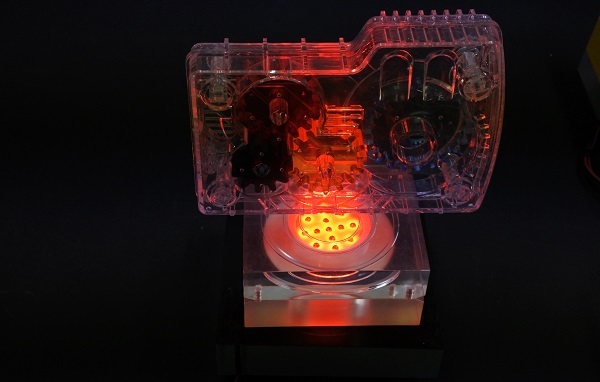
その時期の課題を丁稚として乗り越えると相談だけを待つ見守り
コーティングで良いのだと思います。
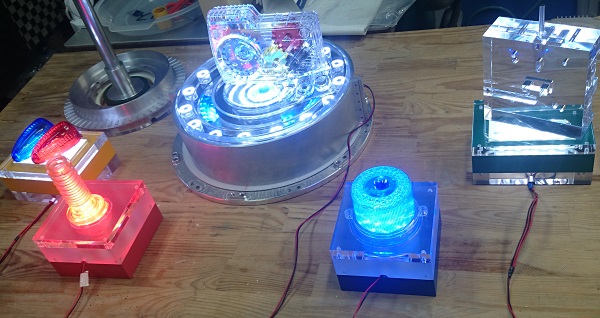
あたらしい課題になると、コントロール(ティーチング)からスタート。
理解が深まるごとにマネジメント(コーティング)に変えていく。
その割合を、その時にベストマッチングさせられると、上手に
育成できるのではないかと思います。
優れた開発ものづくりができるプロのエンジニア&職人を育て、
後世に開発ものづくりのDNAを伝承していく。
それが開発ものづくりアリスの使命だと考えています。
高精度な機械加工にプラスワンする手加工で仕上げる
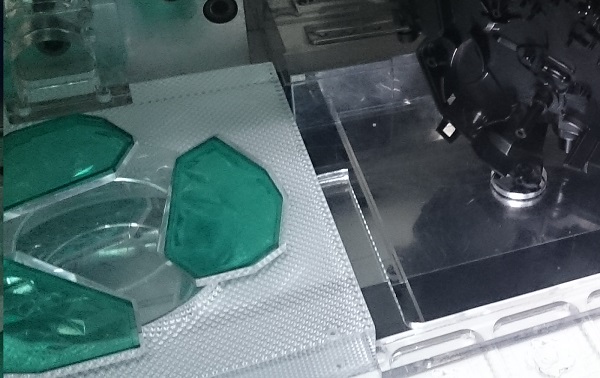
オール機械加工で仕上がる部品はたとえ多面加工であっても最新の
CAD/CAMやコンピューター数値制御で動く工作機械があれば
製作できます。
それはそれで奥深く、技術の追求をすべき点が多々ありますが、
機械加工だけで製作できない部品がもっとも難易度が高いと思います。
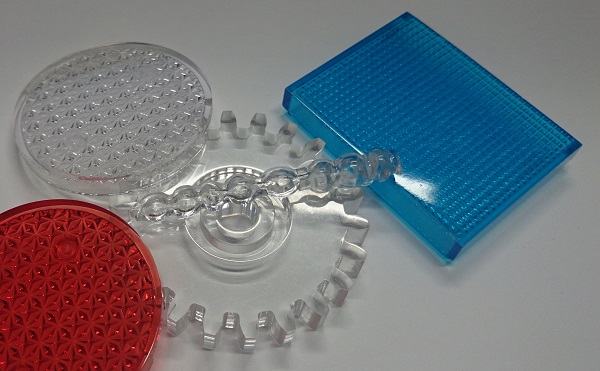
画像のレンズカット加工品では、レンズカット部が難しいと思いがち
ですが、機械が加工するので精度よく製作することは普通にできます。
ギアや飾りなども同じく、機械任せでプログラマーなら誰にでも製作できます。
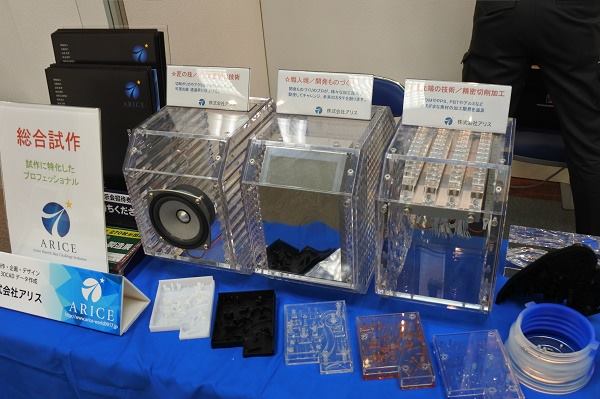
高精度を実現する機械加工はできて当然です。
また磨きや接着、溶着や曲げなどの手加工も同じくプロフェッショナル
であれば、できて当たり前の技術です。
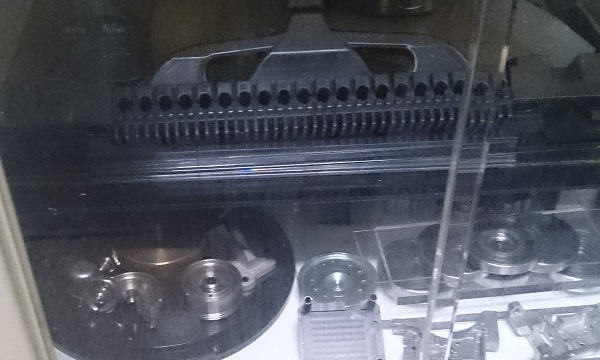
高精度の機械加工品をより高品質にできる技術があって初めて特化
できます。
機械加工技術の追求と同時に手加工の技術を追求する事で、デジタルと
アナログをそれぞれ特化させる事で他社にはできない仕事ができます。
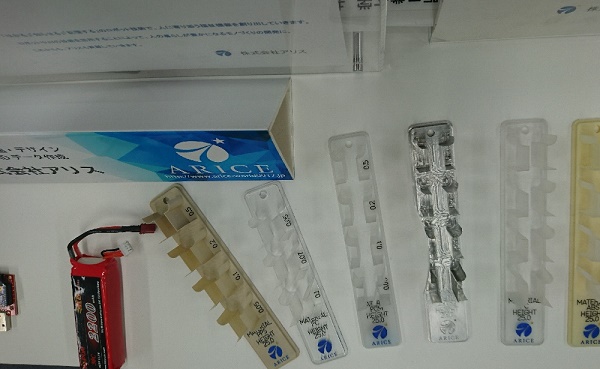
当然、素晴らしいデジタル&アナログの技術を使いこなす思考力や
知恵・経験や発想力などが基礎に必要ですが。
開発ものづくりに関しましては、お気軽にお声かけ下さい。
シンプルな簡易治具で機能を満たす
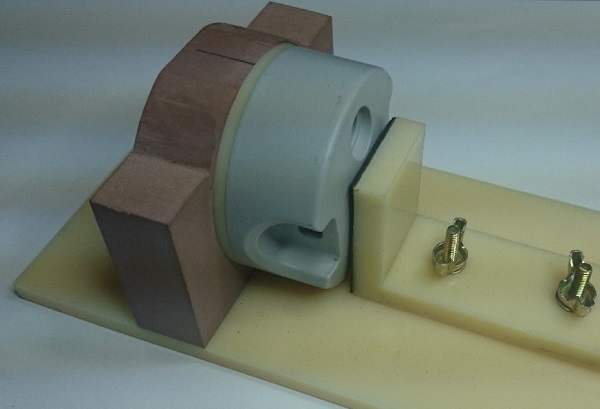
これは、回転シルク印刷用に製作した簡易治具です。
数量が20個未満と少なく、本格的な治具製作によるシルク印刷が
できず簡易治具を考えました。
費用が掛けられない小ロットの部品加工では、手刷りのシルク印刷で
対応することになります。
品質は、量産部品とまったく変わりません。
数量が増えてもコストが大幅に下がらないだけの差です。
切削加工では、こういった簡易治具を製作して機械加工しています。
寸法精度の厳しい機能部品を、高精度で加工するために創る治具。
見栄えは悪くともポイントはしっかりおさえています。
こういった治具を思考して創る能力が、開発ものづくりでは技術力の
差となります。
ホンダ・ズーマーのカスタムパーツ焼付塗装
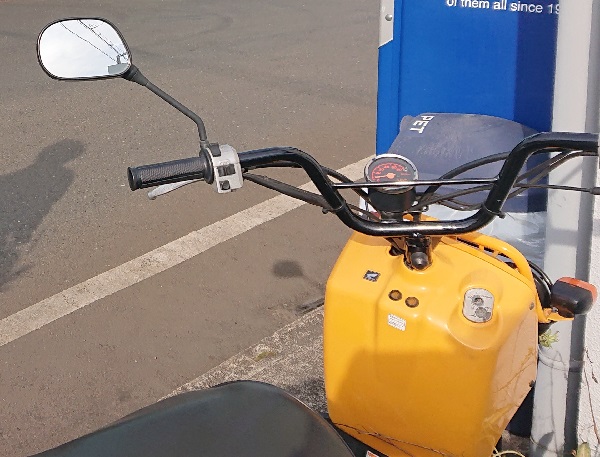
先日、バイクのカスタマイズパーツを製造販売されている
お客様から いただいたホンダ・ズーマーのカスタマイズパーツ。
純正品のようにフィットします。
素材は、軽くて丈夫なCFRP。
これでズーマーが、メットインに進化致します。
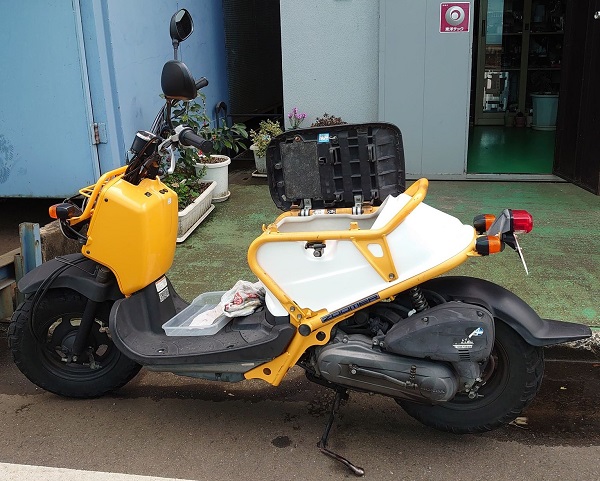
真っ白は塗装前に見えるので、早速焼付塗装をしてもらいました。
色は、ブロンズの光沢メタリック。
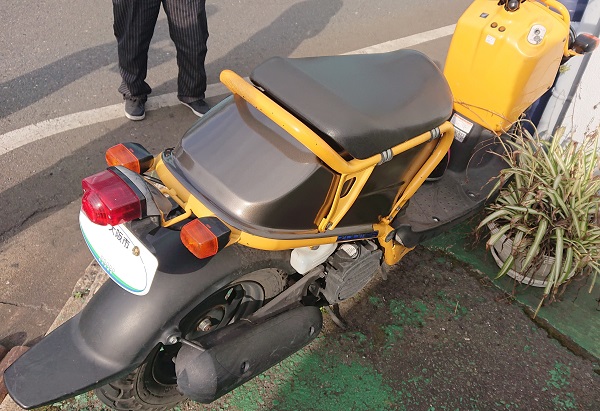
デザインのポイントであるワイルド感を無くさないよう、
カスタム パーツを主張させ過ぎないようにしました。
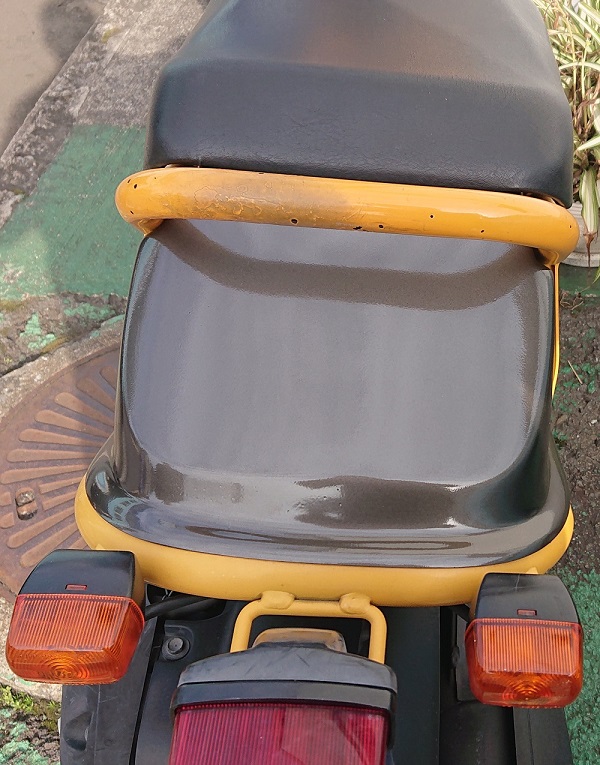
パイプフレームに特徴があるバイクなので、パイプフレームの
存在が消えないようにできたのではないかと思います。
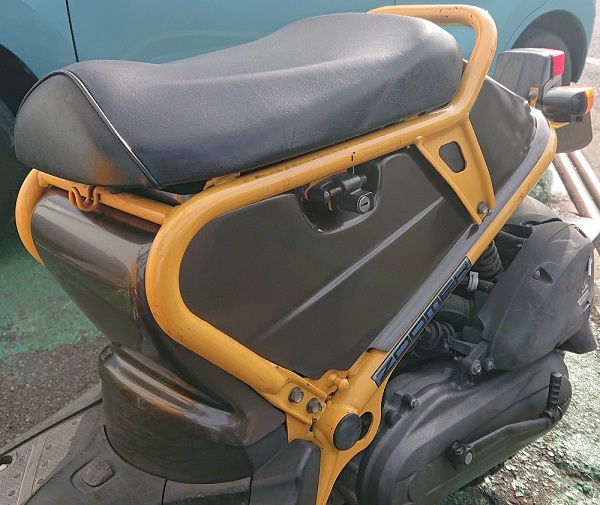
車でよく使われているブロンズ色ですが、バイクでは希少価値が
高いのではないかと思います。
ガンメタとシルバーメタリックも候補として上がりましたが、
ブロンズ色を選んで正解だったと思います。
これも、私たち(株)アリスのお仕事です。
デザインの肝となるパイプフレームの存在感を残せたのが
良かったのではないかと思います。
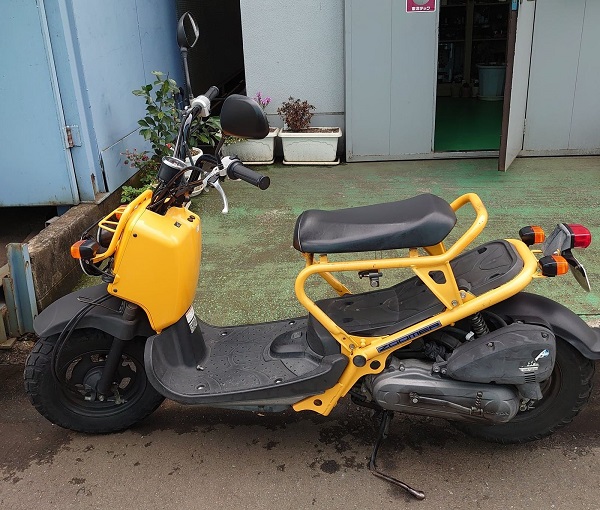
本来はパテ埋めも行うのですが、今回は持ち主がそこまでこだわらず。
ホンダ・ズーマーは、ワイルドでスタイリッシュな素晴らしい原チャリ。
カスタマイズパーツの焼付塗装などはお気軽にお声かけ下さい。
設計ミスに強い試作金型で量産試作品サンプル製作
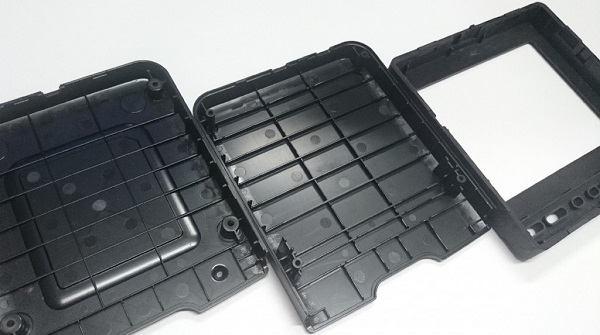
開発ものづくりのアリスでは、プラスチック樹脂の数量が多い試作は
試作金型を使ってのインジェクション射出成形で製作します。
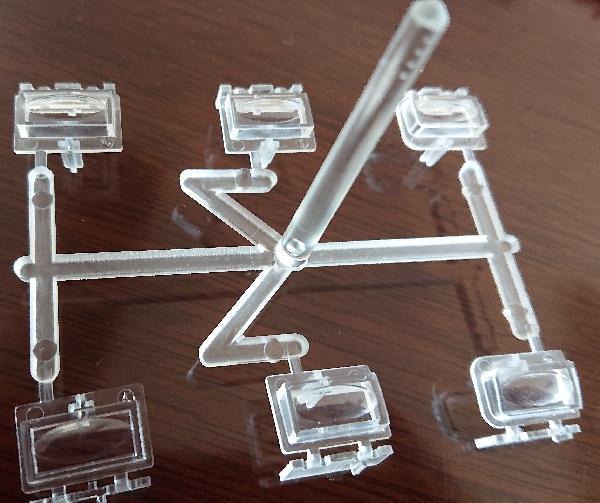
試作板金なども含めたご依頼にも対応可能です。
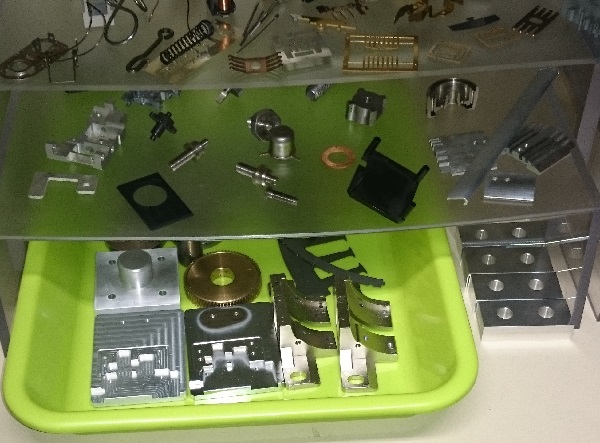
量産プロセスのスムーズな立ち上げに役立ちます。
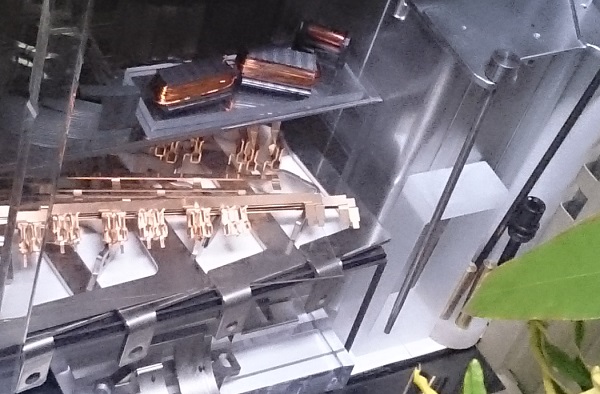
試作金型の特徴は設計ミスや改造にスピーディーな対応ができること。
試作金型の改造スピードには自信がございます。
また変更前の成形品に追加工や改造をして対応することもできます。
プラスチック樹脂部品の量産試作品サンプルは、ぜひお声かけ下さい。
TPX(ポリメチルペンテン)PMP_透明部品の機械加工
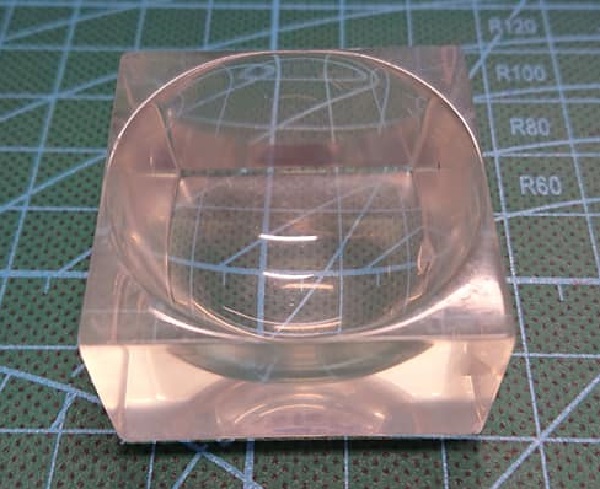
可視化で選ばれることが多いポリメチルペンテン。
数量が少なく、金型の製作費用が出ずに射出成形では製作できない。
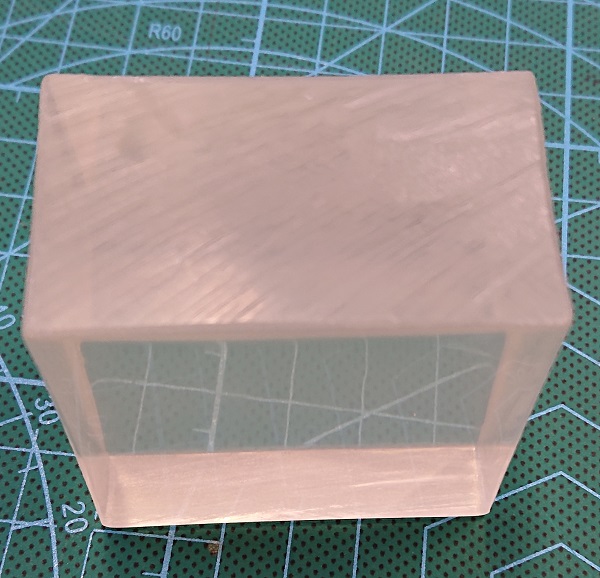
または試作サンプルであり、形状が変わる可能性が高く、金型が
製作できない。
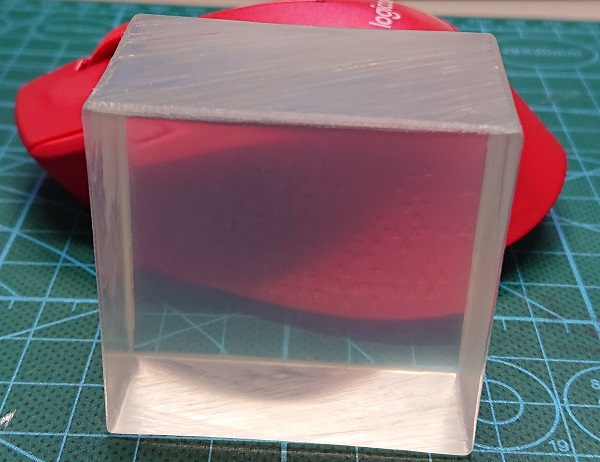
そういった場合は、CNCマシニングセンタや旋盤で切削加工して製作
します。
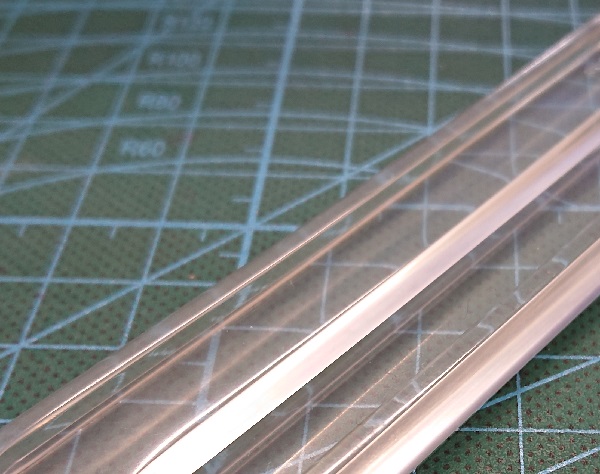
数個から数百個程度であれば機械加工がお得になります。
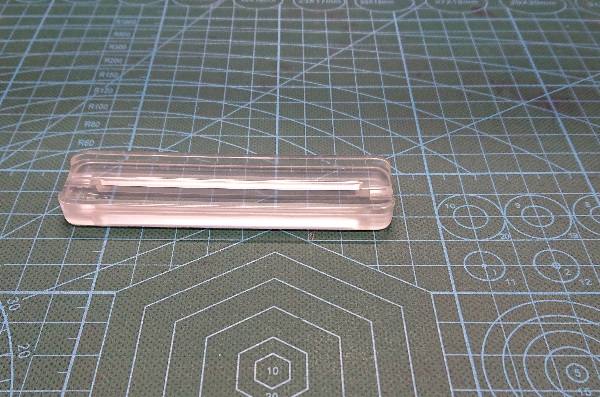
数百個を何度か製作するのであれば金型を製作しての射出成形が
お得かもしれません。
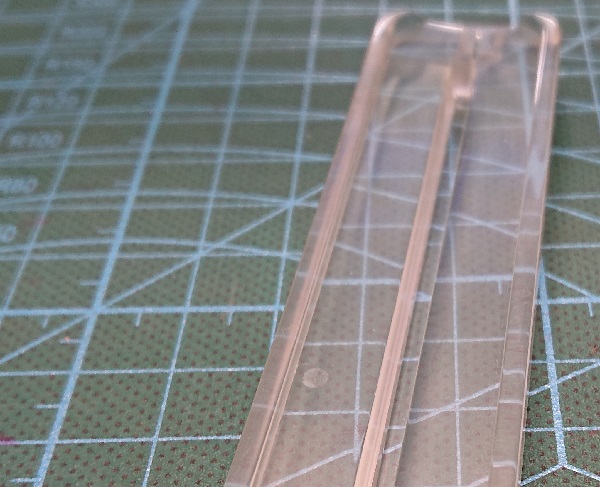
金型を製作した方がメリットが大きい場合は、射出成形で製作
する事も検討させていただきます。
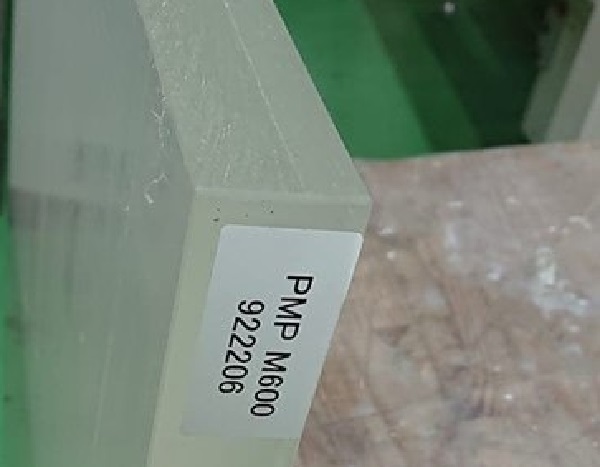
機械加工で製作するか?
射出成形で製作するのか?
形状や数量なども含めてご提案させていただきます。
TPX(ポリメチルペンテン)PMPの部品を製作する場合は、
お気軽にお声かけ下さい。